Metals Industries
Dongbu Steel
Business Environment
Dongbu Steel, as one of the core companies of the East Korea Group, has produced cold-rolled steel sheets in 1967, and since then, through factories in various regions, hot-rolled steel sheets, cold-rolled steel sheets, etc., have an annual scale of about 4 million tons. We produce various steel products. The cold-rolled steel sheet division secured the world's highest competitiveness with the completion of the Asan Bay Plant, which was the first in the world steel industry in 1999 to fully automate the entire process from raw material input to product shipment. Dongbu Steel's electric furnace steel mill was built with a reduced investment in blast furnace capacity, and CO2 emissions and energy consumption were significantly reduced, resulting in high management efficiency and productivity. It is in the limelight as a secured futuristic steelworks. Dongbu Steel is positioned as an integrated steelmaking company that melts pig iron and consistently produces cold-rolled steel sheets, and is making a strong leap toward becoming the world's most competitive steelmaking company. increase.
Project Background & Goals
Customers have the characteristic of purchasing steel products from Dongbu Steel from the inventory list of finished products, just like shopping at a department store. These demand characteristics triggered the risk of eastern steelmaking management. Defective inventories became apparent as raw material and finished goods were provided and inventories increased due to uncertain forecasts. Frequent planning and logistics changes also added to the complexity of production and logistics management. This increased unnecessary operating costs and reduced product quality. Dongbu Steel has determined that in order to survive in the market, it is necessary to redesign the customer-centric process and make quick and accurate decision-making on the system infrastructure based on it. As a solution to this, Dongbu Steel has applied ” Production Seat Reservation Methodology ” to its business. This confirms ” production seats ” to the customer's order, similar to the ticket reservation system where the staff at the counter issues the ticket immediately when booking the ticket. However, it implements a system that promises an order within a fixed time.
Benefits
By applying Zionex's SCM solution to the areas of demand forecasting, delivery date reply, integrated master plan and detailed scheduling, Dongbu Steel will implement a production seating system that considers raw materials and production capacity, and synchronize production, sales and purchase plans. The system has been established. By constructing a raw material preparation system, we upgraded the system that guarantees customer delivery by one step, changed the monthly planning system to a weekly management system, and shortened the lead time. We have established a system that prioritizes inventory processing and built an appropriate inventory management system. In addition, by implementing an ATP (Available to Promise) system, we can promptly return the delivery schedule to the purchase request in charge of demand planning, and make it possible to carry out production planning in the fixed order without delay, which is an epoch-making inventory. Achieved a significant reduction. Material / inventory / resale levels were reduced by 52%, customer response was established within 5 minutes, and average shipping lead times were reduced by 48%.
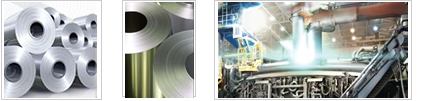
Seah Besteel
Business Environment
Founded in 1937 as Kanto Machinery Mfg. Co., Ltd., SeAH Be Steel is a specialized steel company that manufactures special steel, large forged products, and automobile parts for the automobile and machinery industries. Going forward, we will further expand our business for the high-end specialty steel market overseas, and are aiming for further growth and development through the large-scale forging business used in nuclear power generation, chemical plants and large-scale industrial machinery. As ”Reliable company”, ”Principle-oriented company” Achieve better customer value under thorough customer-centric management “Global leading We are about to become a specialty steel company”.
Project Background & Goals
SeAh Besteel sought to build an integrated sales and production SCM system that would be suitable for high-mix low-volume production methods, yet be capable of agile production planning to meet rapidly changing customer orders. Prior to the introduction of the SCM system, the sales and production departments of Seabe Steel experienced various difficulties. Due to the low delivery date compliance rate, it was not possible to respond to delivery dates in a timely manner, and it was extremely difficult to allocate to process-specific capabilities. In addition, it took time to formulate a company-wide integration plan by manual work using Excel. Not only was information sharing about changes in demand not properly shared, but we also experienced many difficulties such as the inability to flexibly respond to the creation of changed process plans. There are four important goals to be achieved through the construction of the SCM system. First, shorten the lead time for customer service, second, shorten the planned lead time, third, production planning by factory considering optimization of the entire process, and finally, reduce inventory costs, improve equipment availability, and allocate employees. We decided to minimize the replacement.
Benefits
SeAH Besteel, which built the SCP (Supply Chain Planning) system, has improved the manufacturing migration rate by about 90% and the shipping migration rate by about 80% due to the increased efficiency of collaboration between internal and external entities of the company. The timely delivery (on-time delivery) rate has increased by about 90% compared to the past. As a result, we were able to reduce the number of days in stock of raw materials by about 7 days and the number of days in stock of products by about 5 days. In addition, we have made it possible to efficiently utilize resources in the supply chain, reduce unnecessary waste of resources, and flexibly respond to customers' urgent order reception and order changes. In addition, stable production planning has become possible, and the customer's on-time delivery rate has increased, making it possible to create production planning cycles on a daily basis.
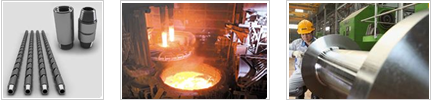