Industria metalúrgica
Acero Dongbu
Entorno empresarial
Dongbu Steel, una de las principales empresas del Grupo Corea del Este, empezó a producir chapas de acero laminadas en frío en 1967 y, desde entonces, a través de fábricas en varias regiones, las chapas de acero laminadas en caliente, las chapas de acero laminadas en frío, etc., alcanzan una escala anual de unos 4 millones de toneladas. Fabricamos diversos productos de acero. La división de chapas de acero laminadas en frío se aseguró la mayor competitividad del mundo con la finalización de la planta de Asan Bay, que fue la primera de la industria siderúrgica mundial en 1999 en automatizar completamente todo el proceso, desde la entrada de la materia prima hasta el envío del producto. La acería de horno eléctrico de Dongbu Steel se construyó con una inversión reducida en capacidad de alto horno, y las emisiones deCO2 y el consumo de energía se redujeron significativamente, lo que se tradujo en una alta eficiencia de gestión y productividad. Está en el candelero como acería futurista asegurada. Dongbu Steel se posiciona como una empresa siderúrgica integrada que funde arrabio y produce sistemáticamente chapas de acero laminadas en frío, y está dando un fuerte salto para convertirse en la empresa siderúrgica más competitiva del mundo. aumentar.
Antecedentes y objetivos del proyecto
Los clientes tienen la característica de comprar productos siderúrgicos de Dongbu Steel a partir de la lista de inventario de productos acabados, como si compraran en unos grandes almacenes. Estas características de la demanda dispararon el riesgo de la gestión siderúrgica oriental. Las existencias defectuosas se hicieron patentes a medida que se suministraban materias primas y productos acabados y aumentaban las existencias debido a la incertidumbre de las previsiones. Los frecuentes cambios de planificación y logística también aumentaron la complejidad de la gestión de la producción y la logística. Esto aumentaba los costes de explotación innecesarios y reducía la calidad del producto. Dongbu Steel ha determinado que, para sobrevivir en el mercado, es necesario rediseñar el proceso centrado en el cliente y tomar decisiones rápidas y precisas sobre la infraestructura del sistema basándose en él. Como solución, Dongbu Steel ha aplicado a su negocio la "Metodología de Reserva de Plazas de Producción". Así se confirman las "plazas de producción" al pedido del cliente, de forma similar al sistema de reserva de billetes en el que el personal del mostrador emite el billete inmediatamente al reservarlo. Sin embargo, aplica un sistema que promete un pedido en un plazo fijo.
Beneficios
Aplicando la solución SCM de Zionex a las áreas de previsión de la demanda, respuesta a las fechas de entrega, plan maestro integrado y programación detallada, Dongbu Steel implantará un sistema de asientos de producción que tenga en cuenta las materias primas y la capacidad de producción, y sincronizará los planes de producción, ventas y compras. Se ha establecido el sistema. Mediante la construcción de un sistema de preparación de materias primas, mejoramos en un paso el sistema que garantiza la entrega al cliente, cambiamos el sistema de planificación mensual por un sistema de gestión semanal y acortamos el plazo de entrega. Hemos establecido un sistema que prioriza el tratamiento de las existencias y creado un sistema adecuado de gestión de inventarios. Además, al implantar un sistema ATP (Available to Promise), podemos devolver puntualmente el programa de entrega a la solicitud de compra encargada de la planificación de la demanda, y hacer posible llevar a cabo sin demora la planificación de la producción en el pedido fijo, lo que constituye un inventario de los que hacen época. Se ha logrado una reducción significativa. Los niveles de material / inventario / reventa se redujeron en un 52%, la respuesta al cliente se estableció en 5 minutos y los plazos medios de envío se redujeron en un 48%.
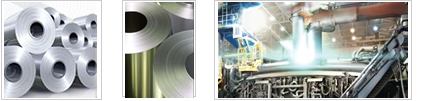
Seah Besteel
Entorno empresarial
Fundada en 1937 como Kanto Machinery Mfg. Co., Ltd., SeAH Be Steel es una empresa siderúrgica especializada que fabrica aceros especiales, grandes productos forjados y piezas de automóvil para las industrias del automóvil y la maquinaria. En el futuro, seguiremos ampliando nuestro negocio en el mercado de aceros especiales de gama alta en el extranjero, y aspiramos a un mayor crecimiento y desarrollo a través del negocio de forja a gran escala utilizado en la generación de energía nuclear, plantas químicas y maquinaria industrial a gran escala. Como "Empresa fiable", "Empresa orientada a los principios" Lograr un mejor valor para el cliente bajo una minuciosa gestión centrada en el cliente "Líder mundial Estamos a punto de convertirnos en una empresa siderúrgica especializada".
Antecedentes y objetivos del proyecto
SeAh Besteel buscaba crear un sistema SCM integrado de ventas y producción que fuera adecuado para métodos de producción de gran mezcla y bajo volumen, pero capaz de planificar la producción de forma ágil para satisfacer los pedidos de los clientes, que cambian con rapidez. Antes de la introducción del sistema SCM, los departamentos de ventas y producción de Seabe Steel experimentaban diversas dificultades. Debido a la baja tasa de cumplimiento de las fechas de entrega, no fue posible responder a las fechas de entrega a tiempo, y resultó extremadamente difícil asignarlas a capacidades específicas del proceso. Además, se tardó tiempo en formular un plan de integración para toda la empresa mediante trabajo manual con Excel. No sólo no se compartía adecuadamente la información sobre los cambios en la demanda, sino que se experimentaban muchas dificultades, como la incapacidad de responder con flexibilidad a la creación de planes de procesos modificados. Hay cuatro objetivos importantes que deben alcanzarse mediante la construcción del sistema SCM. En primer lugar, acortar el plazo de atención al cliente; en segundo lugar, acortar el plazo de entrega previsto; en tercer lugar, planificar la producción por fábrica teniendo en cuenta la optimización de todo el proceso; y, por último, reducir los costes de inventario, mejorar la disponibilidad de equipos y asignar empleados. Decidimos minimizar la sustitución.
Beneficios
SeAH Besteel, que construyó el sistema SCP (Supply Chain Planning), ha mejorado la tasa de migración de fabricación en torno al 90% y la tasa de migración de envíos en torno al 80% gracias a la mayor eficacia de la colaboración entre entidades internas y externas de la empresa. El índice de puntualidad (entrega a tiempo) ha aumentado en torno al 90% en comparación con el pasado. Como resultado, pudimos reducir el número de días de existencias de materias primas en unos 7 días y el número de días de existencias de productos en unos 5 días. Además, hemos conseguido utilizar eficazmente los recursos de la cadena de suministro, reducir el despilfarro innecesario de recursos y responder con flexibilidad a la recepción urgente de pedidos y a los cambios de pedido de los clientes. Además, se ha hecho posible una planificación estable de la producción y ha aumentado el índice de puntualidad de las entregas a los clientes, lo que permite crear ciclos de planificación de la producción diarios.
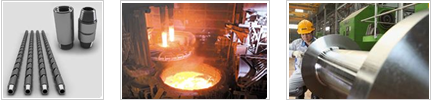