LS Industrial Systems
Business Environment
LS Industrial Systems, a subsidiary of the LS Group, is a leading provider of industrial power equipment and automation equipment. LS Industrial Systems holds the largest market share in Korea and specializes in a range of low-voltage equipment, including circuit breakers and magnetic contactors, high-voltage equipment such as VCBs and mold transformers, and specialized high-voltage power systems like switchgear, RMU, and GIS. In addition, the company has diversified into the rapidly growing industry of photovoltaic power generation, offering products such as inverters, PLCs, and HMIs. Furthermore, LS Industrial Systems has also ventured into emerging fields such as EVs and RFID.
Project Background & Goals
Under the demanding conditions of individual build-to-order businesses such as plant equipment, the process of completing projects, from the estimation of inquiries to design, production, and installation, is carried out as project-based work. To ensure efficient planning and procurement of equipment and resources from both internal and external partner companies, it is crucial to effectively communicate and promptly proceed. Additionally, cost control and profitability for the order amount is a critical mission that must be upheld at all times. To address these challenges, LS Industrial Systems has implemented the Dynamic Task Manager, a solution that enables (1) integrated management of schedules and costs, (2) project cost management through linking with the ERP system, and (3) a progress monitoring function for the entire project, thus ensuring the successful completion of projects.
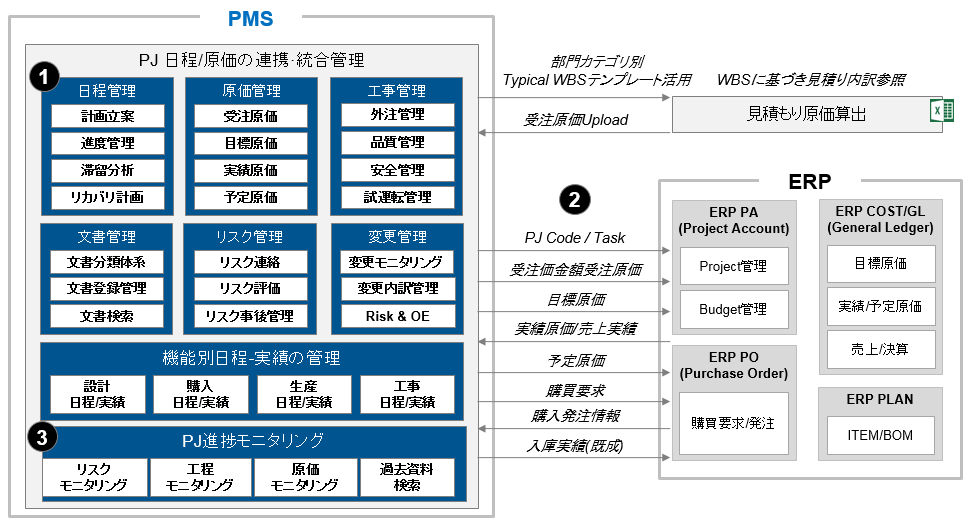
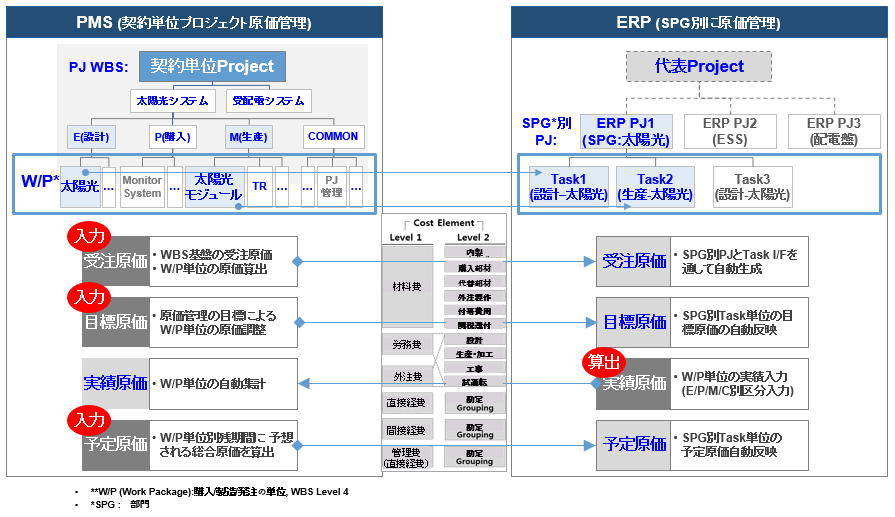
To enhance the management of build-to-order projects, such as plant equipment, we have implemented a comprehensive system using the Dynamic Task Manager. This system allows for the clear definition of the management level of WBS (work breakdown structure) with the fourth level as "Work Package". Each Work Package is responsible for managing procurement, manufacturing, and cost, with the ability to set and track "order cost," "target cost," and "planned cost" and link it to the task managed by our ERP system. This allows for real-time tracking of actual results entered by each SPG (department) and adjusting the "planned cost" to match the target cost.
Additionally, we have created a progress monitoring function for the entire project, allowing the project manager to track the ordering process, gate and phase information of each project by SPG (department) and stay informed of the schedule of the entire project. This system also enables us to identify and mitigate cost risks, ensuring that the project is completed on time and within budget.
Return on Investments
By implementing a shared and visual platform for work processes, we have connected individual efforts on a single database. This allows not only project managers, but also individual engineers, to view and confirm each other's work. This enables cross-departmental and inter-departmental process management, fostering a collective management mindset among all team members.
Furthermore, by providing an Earned Value Management (EVM) chart, we have enabled early identification and management of cost overrun risks, and have created a system that not only supports project planning and progress management, but also budget and cost management across departments. Despite the comprehensive nature of this system, we were able to complete its implementation within a period of approximately 10 months.