Industrias pesadas
Resumen
Kawasaki Heavy Industries : Robot industrial
Kawasaki Heavy Industries fue la primera empresa japonesa en desarrollar y fabricar robots industriales domésticos, y desde entonces ha sido uno de los principales fabricantes de robots que apoyan la automatización en diversos campos de fabricación. Los robots de Kawasaki realizan trabajos de automatización de alta calidad que se adaptan a los requisitos de cada producto y línea de producción, como la soldadura de carrocerías de automóviles y el procesamiento de alimentos.
Antecedentes y objetivos del proyecto
En cada equipo del Robot Business Center, un PM se encarga siempre de varios proyectos de diseño y desarrollo, por lo que resultaba difícil planificar el proyecto, gestionar los recursos de personal y subcontratar. Con el fin de reducir las horas de trabajo de los gestores y mejorar el nivel de gestión, se ha convertido en una cuestión urgente permitir que las partes relacionadas compartan sin demora la información del proyecto y gestionen el progreso desde ubicaciones remotas.
Enfoque del proyecto
Utilizando Aras Innovator, que se ha convertido en el PLM estándar dentro de Kawasaki Heavy Industries, como plataforma, decidimos construirlo utilizando DTM, que es un paquete que amplía la función PM de Aras. Desde el principio, el representante del equipo participó en la evaluación, y con el apoyo del jefe de representantes de usuarios y el personal informático del centro de negocios del robot, ampliamos las funciones y realizamos los requisitos necesarios para nuestra empresa.
Beneficios
A partir de las consultas de los clientes, los PM y los responsables de desarrollo registran la información del proyecto y sus planes en DTM, confirman la carga de personal, asignan al responsable principal y crean un plan. Una vez finalizado el plan resultante del DTM en consulta con el cliente, se notifica diariamente al trabajador el trabajo asignado y el PM puede captar el progreso en el momento oportuno registrando los resultados reales. aumentar. Gracias a este mecanismo, fue posible gestionar sin problemas los proyectos en curso sin intercambios frecuentes de correos electrónicos, y se demostraron los efectos de la reducción de las horas de trabajo de gestión de los PM y la mejora de la tasa de cumplimiento de los hitos.
Sistemas industriales LS
Entorno empresarial
LS Industrial Systems pertenece al Grupo LS (un grupo de 17 empresas, como LS Cable & System y LS Nikko Copper Tube), que se escindió del Grupo LG, famoso internacionalmente como empresa chaebol coreana, y se dedica a equipos de energía industrial y equipos de automatización. Como empresa responsable del sector, tenemos la mayor cuota de Corea. También nos ocupamos de equipos de baja tensión, como disyuntores y contactores magnéticos, equipos de alta tensión, como VCB y transformadores de molde, y sistemas eléctricos especiales de alta tensión, como aparamenta, RMU y GIS. En equipos de automatización, nos hemos introducido en el sector de la generación de energía fotovoltaica, de rápido crecimiento, incluidos inversores, PLC y HMI, y también hemos entrado en campos como los vehículos eléctricos y la RFID.
Antecedentes y objetivos del proyecto
En el negocio individual de construcción bajo pedido, como el equipamiento de plantas, el proceso que va desde la estimación de consultas sobre proyectos hasta el diseño, la producción y la instalación se lleva a cabo como un trabajo de tipo proyecto, y la planificación del proceso se realiza mientras se adquieren equipos y recursos no sólo internos, sino también de empresas asociadas externas. Es esencial informarse a fondo y proceder sin demora. Además, el control de costes y la rentabilidad por el importe del pedido es una misión que debe protegerse en cualquier caso.
Bajo estas estrictas condiciones, utilizando Dynamic Task Manager, hemos construido una función para (1) la gestión integrada de calendarios y costes, (2) la gestión de costes del proyecto mediante la vinculación del sistema ERP, y (3) la función de seguimiento del progreso para todo el proyecto.
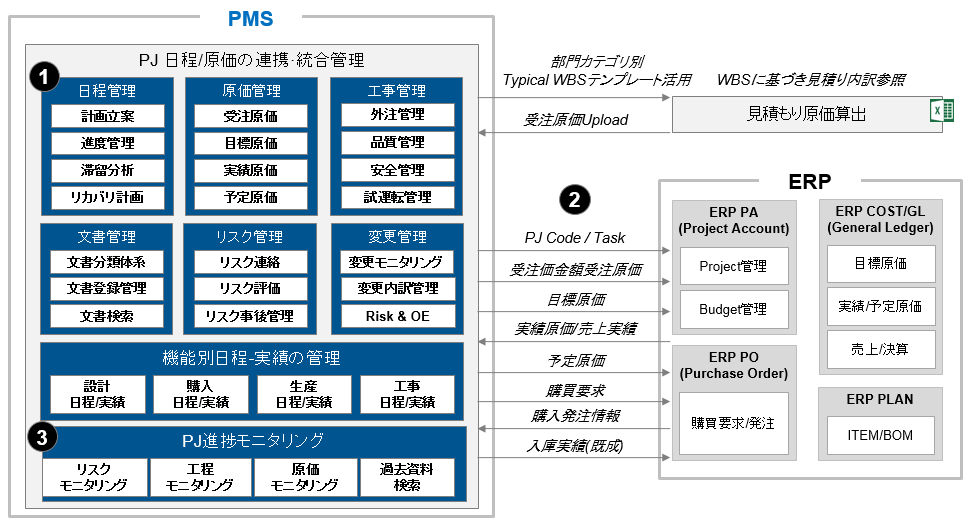
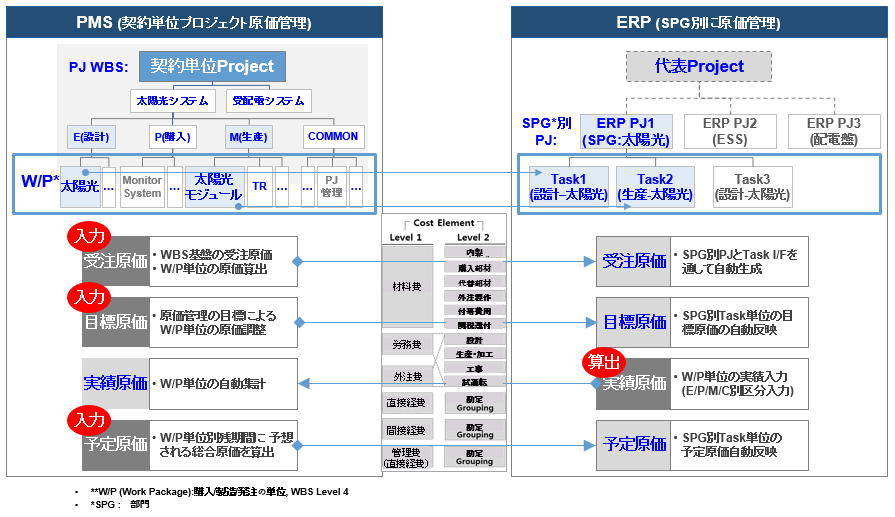
Definir el nivel de gestión de la EDT (unidad de agregación de actividades), posicionar claramente el 4º nivel como "Paquete de Trabajo", gestionar el aprovisionamiento, la fabricación y el coste en esa unidad, "coste de pedido" "coste objetivo" " Establecer el "coste planificado" y vincularlo con la Tarea gestionada por ERP. Por lo tanto, en ERP, es posible agregar los resultados reales introducidos para cada SPG (departamento) y ajustar el "coste planificado" haciéndolo coincidir con el coste objetivo.
Para controlar el progreso de todo el proyecto, desde la planificación hasta el final del proyecto, es posible comprobar la información del proceso de pedido / Puerta / fase de cada proyecto por SPG (departamento), y el gestor del proyecto está informado del calendario de todo el proyecto. Hemos creado un sistema que permite controlar los avances y los riesgos de costes.
Beneficios
Al compartir y visualizar el proceso de trabajo en curso y utilizar una plataforma común, el trabajo realizado individualmente puede conectarse en una base de datos, y no sólo el jefe de proyecto, sino también los ingenieros individuales pueden confirmar el trabajo de los demás. Al mismo tiempo, hemos hecho posible la gestión de procesos entre departamentos y departamentos, donde cada persona puede trabajar con conciencia de gestión prestando atención a la gestión global.
Además, al proporcionar un gráfico EVM, es posible respaldar la toma de decisiones de modo que el riesgo de rebasamiento de costes pueda reconocerse y tratarse en una fase temprana, y puede utilizarse no sólo para la planificación de proyectos y la gestión del progreso, sino también para los departamentos de gestión de presupuestos y costes. Fue construido. A pesar de la construcción a tan gran escala del sistema, conseguimos liberarlo en un plazo de unos 10 meses desde su puesta en marcha.
Doosan Heavy Industries
Entorno empresarial
Doosan Heavy Industries es una empresa integral de industria pesada perteneciente al grupo corporativo Doosan de Corea del Sur, que produce equipos de generación de energía, equipos de planta, equipos de infraestructura, etc., y es responsable de la construcción de grandes plantas y centrales eléctricas en el extranjero, como Arabia Saudí e India. Una empresa global de EPC.
Antecedentes y objetivos del proyecto
Los trabajos de diseño y desarrollo de las instalaciones de centrales eléctricas y turbinas de Doosan Heavy Industries se realizan por encargo individual, y existen problemas que dificultan la expansión del negocio, como la descentralización de diversos datos de ingeniería, la personalización del proceso de diseño y la invisibilidad del calendario de diseño. Lo estaba sosteniendo. Para mantener la competitividad de costes, es esencial mejorar la eficiencia operativa y garantizar la calidad, pero el proceso es complicado para ampliar proyectos y cumplir leyes y normativas estrictas, y tenemos que confiar en las habilidades y el ingenio individuales. En estas circunstancias, era difícil adaptar el sistema PLM que soporta el método convencional de ensamblaje de piezas. Por ello, en previsión de futuros cambios, decidimos construir un sistema utilizando el método de desarrollo SI basado en la plataforma Aras, que garantiza escalabilidad y flexibilidad.
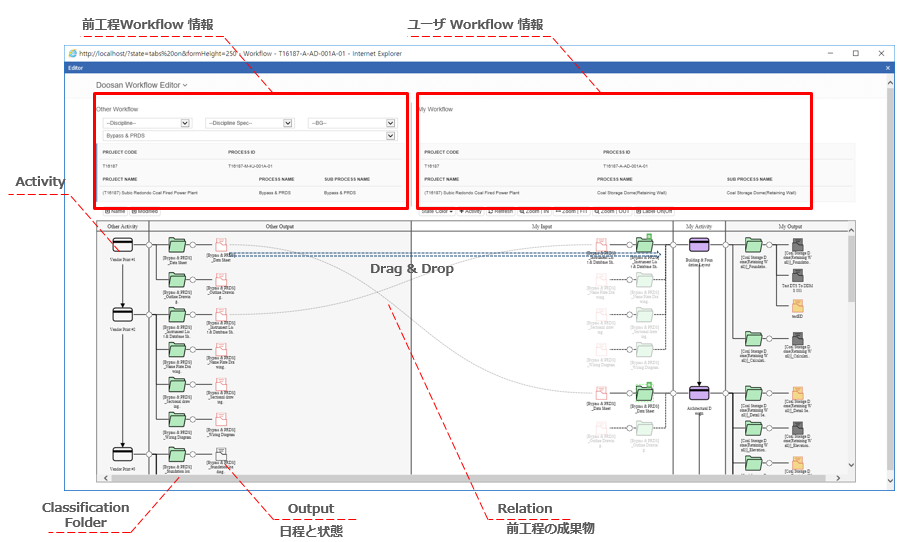
En primer lugar, nos propusimos "normalizar el proceso de diseño" para llevar a cabo el procedimiento de diseño con precisión, y para ello definimos un proceso estándar en función del tipo de proyecto y lo gestionamos en la base de datos como una plantilla de flujo de trabajo estándar. Las tareas del flujo de trabajo se definen junto con la programación del proyecto mediante el complemento Dynamic Task Manager de Aras Innovator, y los diagramas de Gantt se utilizan para compartir la programación.
A continuación, con el fin de gestionar sistemáticamente la información de especificación de equipos y aparatos, se utiliza la base de datos de ingeniería, se define la clasificación estándar de equipos y aparatos (plantilla de equipos) y se proporciona a cada uno la información de especificación y la información de modelado. , se convierte en una biblioteca de equipos e importa esta información para crear modelados 3D. Los valores de los atributos necesarios para la gestión se asignan a cada dispositivo, y los derechos de acceso también se establecen para cada lista o elemento.
Beneficios
Al definir los flujos de trabajo y normalizar los procesos empresariales, se construyó la esencia de un entorno de diseño integrado. Para ejecutar a fondo el proceso de diseño según el flujo de trabajo, hemos desarrollado y proporcionado un editor que asocia actividades y entregables con una función de dibujo de definición del flujo de trabajo fácil de usar y una pantalla de gestión gráfica para que todos los usuarios puedan utilizarlo sin resistencia. Sí. Como resultado, se visualiza el procedimiento empresarial y es posible comprender intuitivamente la relación entre el estado empresarial y el documento.
Dado que la información sobre especificaciones puede gestionarse sistemáticamente utilizando la biblioteca de equipos y la BD de ingeniería, la cantidad de materiales y equipos necesarios se calcula mediante modelado 3D, que es la fuente de datos para la adquisición de equipos, la construcción y la producción, así como para proyectos similares. También era posible reutilizarlo para la estimación.
El portal de ingeniería permite a las partes interesadas compartir actualizaciones a tiempo y mejorar la integridad del diseño. Todas las partes pueden utilizar esta página del portal para los procedimientos de entrega / solicitud y registro de datos, la información relacionada con ellos se actualiza constantemente como un nuevo feed, y el estado del proyecto se puede comprobar en el tablero de instrumentos.
Actualmente, seguimos colaborando con SCM para prestar apoyo a una amplia gama de carteras.
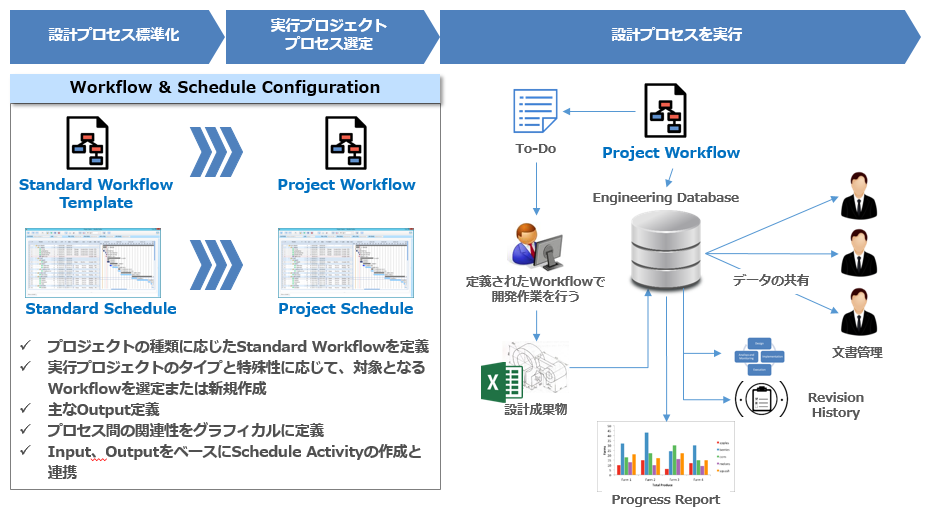
Hanwha Techwin
Entorno empresarial
Desde que inició el negocio de motores de aviación y cámaras en 1977, Hanwha Techwin ha desempeñado un importante papel en el desarrollo de la industria de maquinaria de precisión, ampliando su ámbito de negocio a piezas de equipos de fabricación de semiconductores, turbocompresores, artillería autopropulsada, etc. Sí. También fabricamos productos de alta tecnología, como equipos de información por vídeo que requieren tecnología punta en la era multimedia. Hanwha Techwin está a punto de dar un salto adelante como líder mundial en Seguridad y Energía caso 04 con la mejor tecnología en el campo de la maquinaria de precisión. En concreto, la División de Sistemas de Potencia se encarga de los negocios de motores de aviación, piezas de motores y equipos de energía.
Antecedentes y objetivos del proyecto
La división Power Systems de Hanwha Techwin, que ha introducido la solución SCM proporcionada por Zionex, es compatible con el método de producción ETO (Engineer To Order). El método ETO, es decir, la "estrategia de producción de diseños personalizados", es un método de producción con el diseño individual solicitado por cada cliente al hacer un pedido. En la estrategia ETO, también se denomina "método de proyectos" porque tiene las características de la producción por encargo a gran escala. En aquel momento, Hanwha Techwin tenía un plazo de entrega al cliente más largo debido al innecesario tiempo de espera en el patio, y los planes no se sincronizaban sistemáticamente entre las fábricas. También tuvimos problemas, como la imposibilidad de responder con prontitud a los pedidos y los cambios en las especificaciones. Para resolver estos problemas y mejorar la reducción de inventarios y la tasa de entrega a tiempo al cliente, Hanwha Techwin ha seleccionado e iniciado un proyecto para implantar la solución SCM de Zionex. Lo que pretendíamos conseguir con el proyecto era establecer un sistema de planificación de la ejecución de la producción semanal y mensual que tuviera en cuenta la capacidad de los equipos y la disponibilidad de material.
Beneficios
Tras introducir la solución SCM, Hanwha Techwin decidió implantar las cuatro siguientes. En primer lugar, la automatización de las tareas de planificación y gestión de la producción. En segundo lugar, establecer un sistema de gestión avanzado mediante la previsión mensual y semanal del estado de carga de los equipos y los niveles de inventario. En tercer lugar, estableciendo un sistema que pueda reformular el plan en el plazo de una hora en función del cambio del plan y sincronizando la información entre la fecha de entrega / plan de producción / calendario de necesidades de material, es posible responder inmediatamente al cambio. Equipado con un sistema. En cuarto lugar, hemos puesto en marcha una herramienta de seguimiento continuo de las comparaciones de rendimiento previstas. Gracias a este proyecto de implantación de la solución SCM, Hanwha Techwin pudo reducir los días de inventario de piezas y mejorar el cumplimiento de la planificación de la producción. También hemos conseguido mejorar la tasa de ejecución de los planes de trabajo diarios en más de un 90%, reduciendo el tiempo de espera de los procesos y el plazo de entrega.
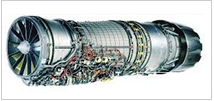
Corea KOSO
Entorno empresarial
Fundada en 1979, Korea KOSO Co. es una empresa propiedad al 100% de Nippon Koso Co. Nippon Koso Co., Ltd. se fundó en 1965 y es líder mundial en el campo de las válvulas industriales de control automatizado. Korea KOSO ensambla válvulas especiales y diversas piezas que requieren tecnología avanzada y las suministra a empresas nacionales de todo el mundo de los sectores de la construcción naval y las plantas industriales.
Antecedentes y objetivos del proyecto
Korea KOSO se enfrentaba entonces a tres grandes retos empresariales: en primer lugar, era necesario sistematizar la gestión de contratos a gran escala con clientes EPC (ingeniería, adquisición y construcción). En segundo lugar, necesitábamos gestionar razonablemente los nuevos diseños de nuestros clientes y sus requisitos de fabricación y, por último, teníamos que implantar un sistema que nos permitiera colaborar con clientes y proveedores de todo el mundo. Además, las válvulas producidas en Corea KOSO son formas de producción DTO (Design To Order) o ETO (Engineer To Order). En este caso, se lleva a cabo una cooperación orgánica y una integración de datos entre procesos que incluyen el desarrollo de productos, las compras y la producción. Es un factor importante de competitividad. Como solución a esta situación, Korea KOSO ha construido un sistema PLSCM promoviendo la innovación de procesos vinculada a la integración de PLM y SCM basada en Aras Innovator, una solución PLM (gestión del ciclo de vida del producto).
Beneficios
En el área de PLM, hemos establecido un sistema de gestión de la información sobre productos e incorporado al sistema PLSCM un proceso de gestión de proyectos basado en la cadena de valor. Además, hemos reforzado nuestras capacidades de QCD (calidad, coste, entrega) y ahora podemos gestionar la lista de materiales (BOM) de toda la empresa. Korea KOSO también promovió la innovación en la cadena de suministro con el objetivo de cumplir los plazos y reducir las existencias, junto con un proceso rápido de toma de decisiones para garantizar la visibilidad de la cadena de suministro. Como resultado, hemos reforzado la base de colaboración con las empresas subcontratadas de la cadena de suministro. Por último, gracias al sistema PLSCM, pudimos mejorar globalmente los procesos y la cadena de valor de la empresa, desde los pedidos hasta el desarrollo, pasando por las compras y la producción. En la función de gestión de ventas, se ha implementado la función de gestión de la información del cliente, la función de gestión de presupuestos y cálculo automático del margen de beneficio, la función de gestión de especificaciones, el diseño, la función de confirmación del progreso de la producción, etc. Las funciones de gestión de ingeniería incluyen funciones de gestión de especificaciones técnicas, funciones de gestión de piezas y listas de materiales y funciones de integración CAD. En el área de control de producción, se implementan funciones de gestión del progreso del diseño para cada válvula, gestión de la operación (Operación) específica de la válvula y funciones de gestión del progreso del trabajo, y en las áreas de compras y calidad, se implementan operaciones (Operación) específicas del departamento. Gestión de la calidad, gestión del progreso de las operaciones, gestión de los informes del departamento de calidad, etc.
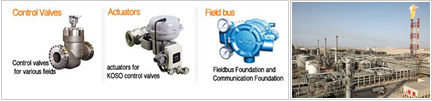